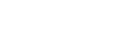
热线电话:
138 8005 8345
机制板聚氨酯胶虽性能卓越,但若施工不当,仍可能导致粘接失效、胶层开裂等问题。据统计,70%的粘接事故源于操作不规范。本文将从基材处理、配胶混合、涂胶压合、固化控制四大环节,结合真实案例,详解施工全流程,并提供五大常见问题的解决方案,助您一次性实现“零缺陷”施工。
基材表面处理:粘接力的根基
金属板材处理:
除锈:使用角磨机或喷砂机清除表面氧化层,粗糙度建议Ra≤3.2μm;
脱脂:用丙酮或专用清洗剂去除油污,确保接触角<30°(水滴测试法)。
芯材处理:
玻镁岩棉、硅岩等需打磨至无浮灰,必要时涂刷界面剂增强附着力。
环境条件控制:
温度:15℃~30℃为最佳施工温度,低于5℃需预热基材或使用暖风机;
湿度:相对湿度≤70%,避免胶层吸潮泛白。
工具与防护装备:
必备工具:高精度电子秤(误差±0.1g)、电动搅拌器、锯齿刮刀、压辊;
安全防护:丁腈手套、护目镜、防毒面具(通风不良时使用)。
主固配比100:20的科学依据
固化剂比例过低(如100:15):胶层无法完全交联,强度下降40%;
固化剂比例过高(如100:25):胶层脆化,耐冲击性降低。
案例:某冷链车厢厂因工人误配为100:18,导致胶层在-30℃下开裂,返工损失超10万元。
混合操作规范
搅拌时间:3~5分钟,直至胶液颜色均一(白色流体变为乳白色),无肉眼可见颗粒;
消泡技巧:
机械消泡:使用真空搅拌机,负压-0.08MPa下脱泡2分钟;
自然消泡:静置5分钟,配合刮刀轻拍胶面排气。
混合后使用时限
开放时间(适用期):常温下10~15分钟,超时后粘接力下降50%;
应急方案:夏季高温时,可将胶桶置于冰袋上延长开放时间至20分钟。
手工施胶工艺
适用场景:小面积粘接、异形板材(如圆弧形防火门);
操作要点:
胶层厚度:0.5~1mm(过厚易收缩,过薄则强度不足);
涂胶速度:10~15cm/s,确保胶线连续无断点。
机器喷涂工艺
设备选型:推荐双组份喷涂机(如Graco XM系列),配比误差≤1%;
参数设置:
喷嘴直径:1.5~2mm;
喷涂压力:0.3~0.5MPa;
走枪速度:1m/s,胶层均匀性误差<5%。
案例:某电子厂5000㎡洁净车间采用机器人喷涂,3天完工,胶缝厚度标准差仅0.1mm。
压合操作规范
压合力:0.2~0.4MPa(可使用气动压机或手动压辊);
压合时间:≥30秒,确保胶液充分浸润基材表面;
错位修正:压合后5分钟内可微调位置,超时需重新涂胶。
温度对固化的影响
理想条件:25℃下,初固时间2小时,完全固化24小时;
低温应对:5℃以下时,每降低10℃,固化时间延长1倍,建议使用红外加热灯;
高温加速:40℃时固化时间缩短至8小时,但需监控胶层收缩应力。
湿度控制
高湿度(>80%)易导致胶层发白,需使用除湿机或延迟施工;
应急处理:已泛白的胶层可用热风枪(60℃)烘烤10分钟恢复透明度。
问题现象 | 根本原因 | 解决方案 |
---|---|---|
胶层发脆开裂 | 固化剂过量或低温未完全固化 | 严格按100:20配比,低温环境延长固化时间 |
粘接面局部脱胶 | 基材清洁不彻底或压合不紧密 | 重新打磨基材,使用夹具加压24小时 |
胶层气泡密集 | 搅拌不均匀或基材孔隙未填充 | 真空脱泡+二次补胶 |
胶液流淌严重 | 开放时间过长或涂胶过厚 | 缩短单次配胶量,胶层厚度控制在1mm以内 |
胶缝泛白起雾 | 湿度过高或固化温度过低 | 使用除湿机,固化温度提升至20℃以上 |
验收指标:
目视检查:胶缝连续无断点,无气泡、杂质;
强度测试:随机取样送检,拉力值≥8000N;
气密性检测(洁净车间):压差500Pa下泄漏率<0.1%。
质保档案:
记录配比、环境参数、操作人员等信息,存档至少5年;
案例:某医药厂因施工档案齐全,胶缝5年后开裂时成功追溯为基材问题,避免责任纠纷。
机制板聚氨酯胶的卓越性能需依托科学施工方能完全释放。通过标准化流程、精细化操作与全过程监控,可显著降低工程风险,提升客户满意度,为企业在激烈竞争中赢得口碑与复购。